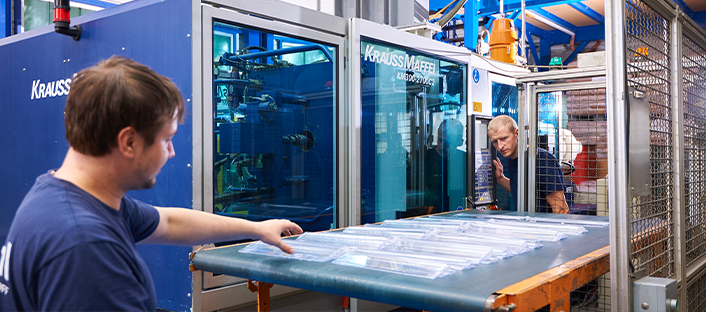

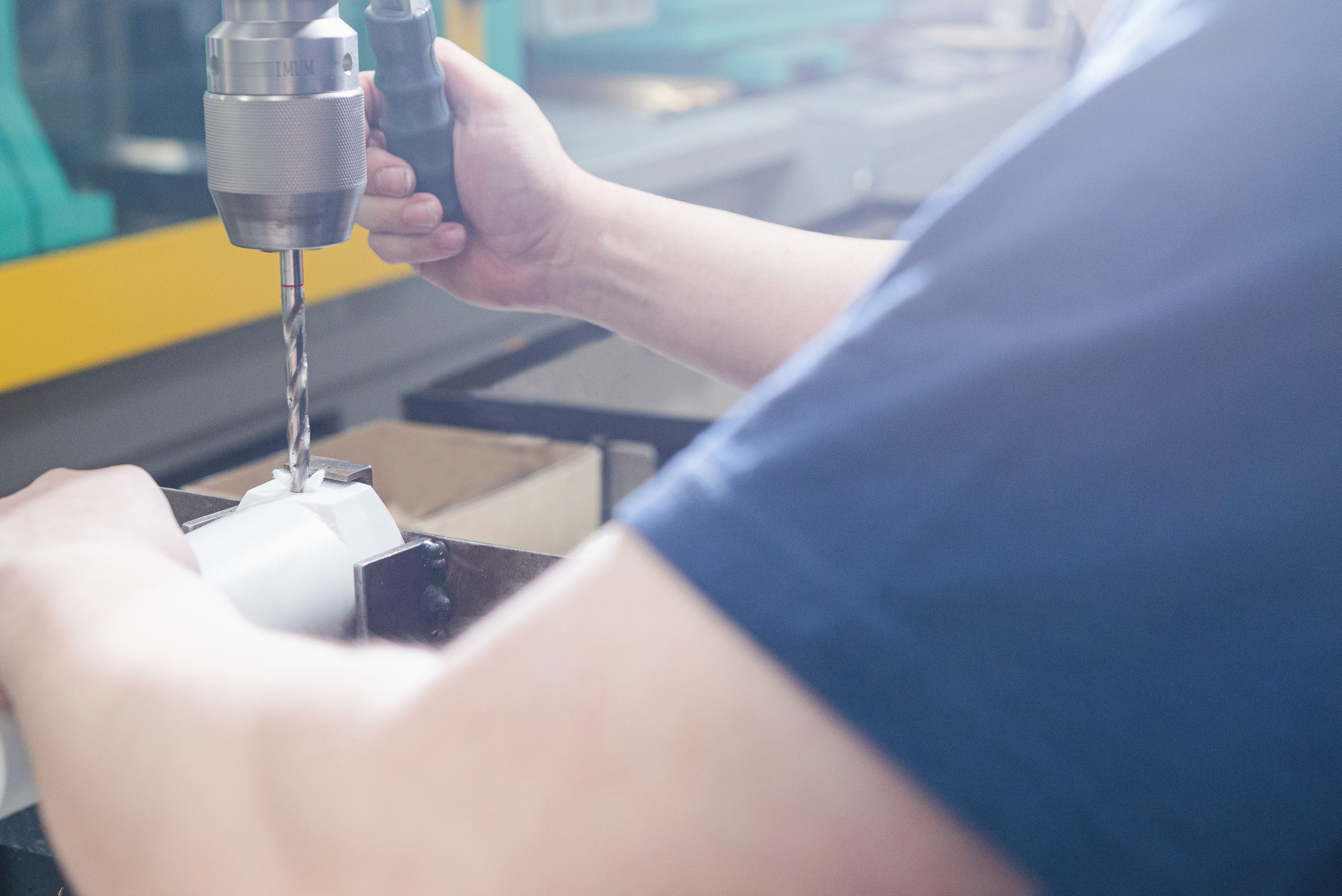
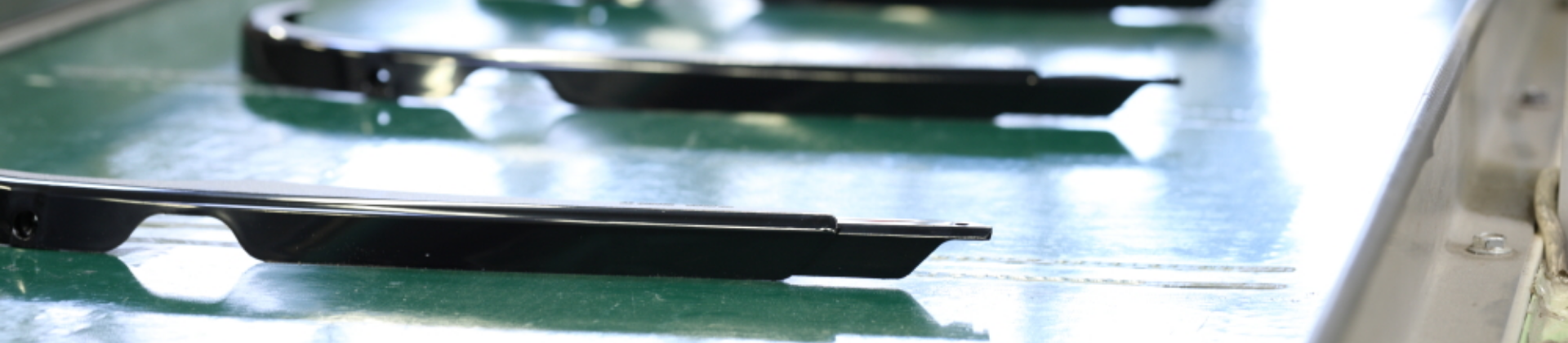
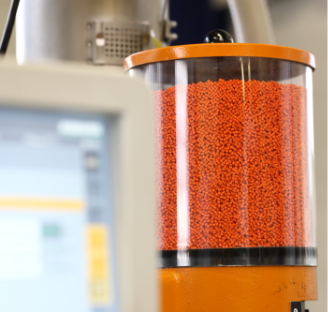
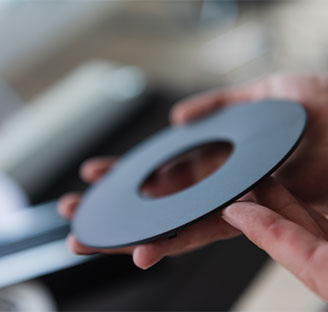
Der Spritzgussprozess
Insgesamt läuft der Kunststoff-Spritzguss in fünf Phasen ab:
1. Die Plastifizierung
In diesem Schritt wird das gewählte Kunststoffgranulat über einen Fördergerät in die Maschine befördert und verflüssigt.
2. Das Verdichten
Durch zunehmenden Druck in der Plastifiziereinheit und durch die sich rotierende Schneckenwelle wird der flüssige Kunststoff verdichtet.
3. Das Einspritzen
Die Form-Hälften werden geschlossen und der Kunststoff über die Auslassdüse eingespritzt.
4. Der Abkühlprozess
Die Form wird gekühlt, meist mittels Wasser, das durch die in der Form liegenden Kühlkanäle geleitet wird. Dadurch wird das Werkstück formstabil.
5. Entformen und Entnahme des Bauteils
Die Werkzeugform wird geöffnet und das Bauteil mittels kleiner Auswerfstifte aus der Form geschoben
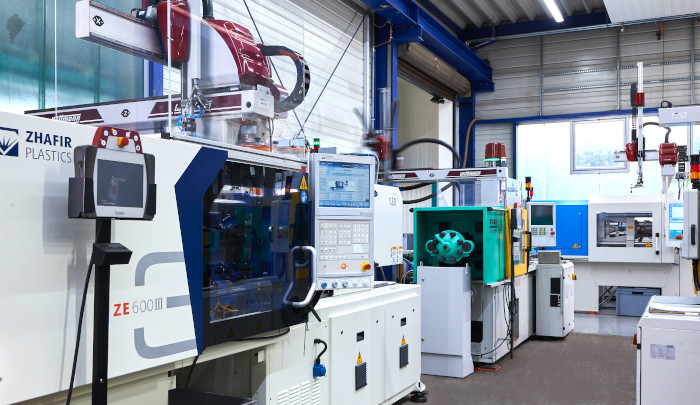
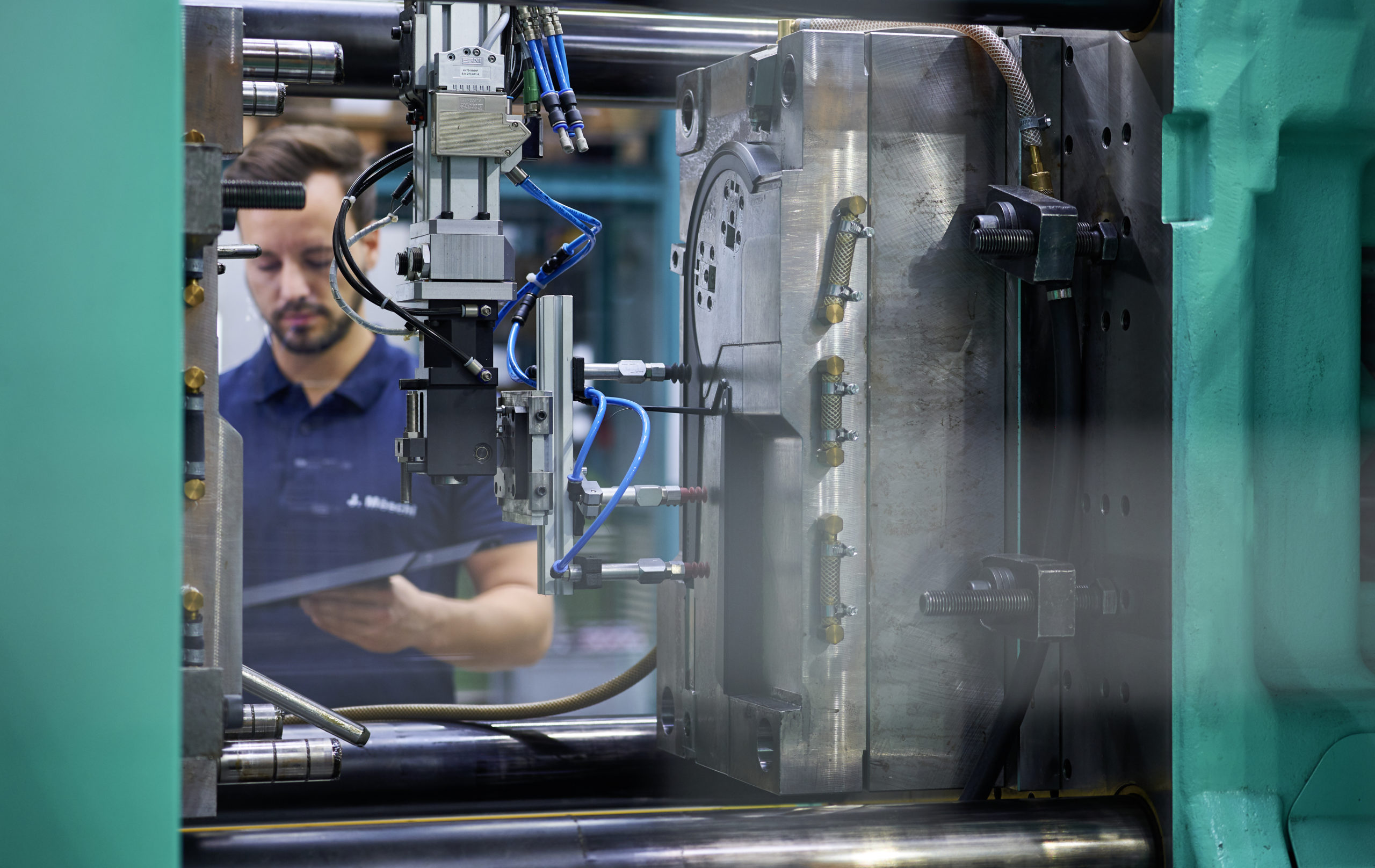
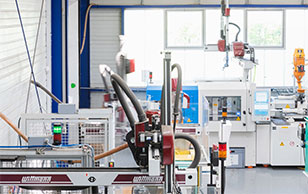
2.300 kWh
Durchschnittliche Stromerzeugung pro Tag
6h / Tag
Durchschnittliche autarke Produktion durch Solarstrom
90 %
Die Kunststoffe werden zur Weiterverarbeitung recycelt
100 %
Engagement für die Umwelt als Firmenphilosophie